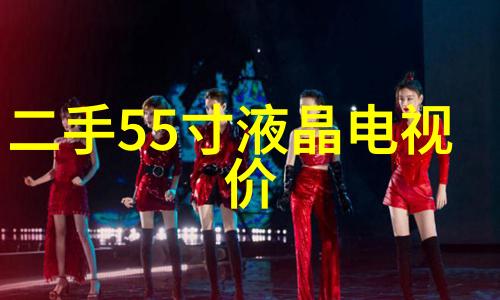
传统Distributed Control SystemDCS与现代PLC对比分析
在工业自动化领域,控制系统的发展史是长达数十年的过程。随着技术的不断进步,我们有了更多种类的控制系统来满足不同的需求。在这篇文章中,我们将专注于比较两种最常见的控制系统:传统Distributed Control System(DCS)和现代Programmable Logic Controller(PLC)。我们将探讨它们各自的特点、优势和局限性,以及它们如何适应不同规模和类型的工业环境。
DCS设备简介
Distributed Control System是一种广泛用于大型工业设施中的控制解决方案。它通过网络连接多个单元,使得整个系统能够有效地协同工作。这使得DCS非常适合那些需要处理复杂流程、跨越多个站点或具有高度动态性的生产环境。
PLC设备简介
另一方面,PLC则是一种更为灵活且经济实惠的小型化控制器,它们通常用于制造业、建筑维护以及其他需要简单自动化任务的地方。这些小型计算机可以编程以执行特定的操作,如开关电气设备或者监控传感器数据。
对比分析
功能性
复杂度 - DCS通常包含更高级别功能,如优化算法、高级数据分析以及强大的模拟能力,这些对于大型工厂来说至关重要。而PLC则主要设计用来执行基本的逻辑操作。
扩展性 - DCS由于其分布式架构,可以轻松扩展以适应不断增长或变化的事务,而PLC可能需要重新配置或升级以匹配新的需求。
可靠性 - 大多数情况下,DCS提供了更高水平的一致性和可靠性,因为它们由专业人员设计并部署。但是,如果不正确配置,任何一台PLC都可能成为故障点。
性能成本
初期投资 - PLCC往往具有较低初始成本,因为它们相对便宜且易于安装。此外,它们也容易找到兼容硬件组件进行升级。
运营成本 - 由于其高度定制化和复杂结构,DCS通常在长期内会产生更高额的心智劳动成本,但它能够实现更加精确细微调整,从而提高效率并降低能源消耗。
易用性与学习曲线
用户界面 - PLCC拥有直观易用的图形界面,让非工程师用户也能进行基本编程,而DCS可能要求用户具备深入了解计算机网络及其协议。
培训与支持 - 虽然二者都有丰富资源供学习,但由于广泛使用的人员熟悉度较高,大部分公司倾向于选择既知晓又熟练掌握的人力资源,以减少学习时间并提高生产效率。
应用场景与行业标准
在化学加工厂中,一家企业可能会选择使用一个完整集成的大型DCS来管理所有反应过程,并确保产品质量符合严格标准。而另一家位于食品加工行业的小企业,则可能只需一个几台PLC就可以完成日常包装、存储等任务。
当涉及到远距离通信时,比如油田管道监测站,那么依赖无线通信方式进行数据交换的是一种非常先进但价格昂贵的大规模智能网格,这里要考虑的是完全基于IT基础设施的一套综合解决方案;而对于某些简单重复性的作业,如水泵房或输送带管理,那么使用本地回路直接连接到现场即可实现最小延迟性能,是一种典型利用现有的物理布线条件去建立最简单直接联系的一个例子。
在建设项目上,对于大楼施工中的机械设备调试管理来说,由于是短暂且一次性的活动,不需要大量持续运行,所以采用PC作为主控中心加上一些继电器作为辅助装置已经足够;然而,在核电站这样的关键基础设施建设中,因安全考量必须保持稳定运行,因此采用分布式系统如dcs是必不可少的手段之一,以保证全方位监控防范措施不会因为单一故障导致灾难发生。
在医疗服务机构中,虽然医疗设备也有很大的自动化需求,但是考虑到医生的专业技能,他们一般偏好手动操作,所以医疗机构并不特别追求自动化程度高,但仍然希望通过一定程度上的信息技术帮助提升诊疗质量,比如记录病人历史记录、药物剂量推荐等功能,这里的决策是否采用dc还是plc取决于具体应用场景及预算限制的情况下做出的决定。”
总结:
在工业自动化领域,无论是老旧传统Distributed Control System还是现代Programmable Logic Controller,每种工具都有其独特之处。当评估哪一种最佳时,要考虑业务需求、预算限制以及所需实施速度。虽然每个组织都寻求最大限度地提高效率,同时减少风险和费用,但正因如此,他们才被迫从众多选项中做出艰难抉择。