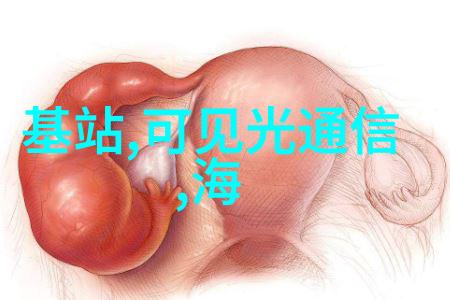
当前的智能制造趋势对工控机电源要求有哪些新的挑战
随着工业4.0和智能制造技术的快速发展,传统的生产模式正在经历深刻变革。自动化、物联网、大数据分析和人工智能等新技术正被广泛应用于各个行业,使得工厂变得更加灵活、高效和智能。然而,这种转型也带来了新的挑战,尤其是在能源管理方面,其中一个关键问题就是如何确保高效稳定的电源供应。
在过去,工业控制系统(ICS)通常采用单一或双重冗余电源解决方案来保证系统连续运行。如果发生主电源故障,可以迅速切换到备用电源以避免生产中断。但是,随着智能制造环境中的设备数量增加,以及这些设备对功率需求提高,对于维持稳定可靠的工作状态就越来越重要了。
首先,我们需要了解什么是工控机电源。在工业自动化环境中,通常指的是为控制器、传感器、执行器以及其他相关设备提供能量的一套系统。这包括了各种类型的交流和直流电源模块,它们能够根据不同的负载需求进行调整,以确保系统正常运行。此外,由于工控机往往位于恶劣环境中,如振动大、温度高或湿度极端,因此它们必须具备足够的抗干扰能力和耐久性。
在这个背景下,当我们谈论当前智能制造趋势时,我们可以看到几个关键点:1) 对实时数据处理速度更快;2) 对通信网络要求更高;3) 对功率密度比更大;4) 对整体能效比要求更严格。为了满足这些新标准,我们需要重新思考我们的工程设计方法,并寻找既符合性能又能节约成本的解决方案。
从功率质量角度考虑,在现代工业自动化中,对频率波动、小幅变化甚至短暂失去信号的情况都不能容忍,因为这可能会导致精密控制失准,从而影响整个生产线乃至整个企业运营的情况。而对于那些涉及到高速运动或者精细操作如打印机械来说,更需要的是不间断且瞬间响应性的供电能力,以确保无任何延迟产生错误输出。
此外,由于物联网技术使得每个部件都成为了信息交互的一部分,其对网络资源利用方式也逐渐演变。因此,不仅要保证物理上的安全,还要关注数字层面的安全性,比如防止未授权访问或潜在攻击者通过网络窃取敏感信息。这意味着除了纯粹的手动调试与监控之外,还需结合远程监测与管理工具,以及实施合适程度的人员培训计划,以便即时应对突发事件并保持业务连续性。
关于绿色节能,一种有效策略是采用超级容错(Super Capacitor)辅助存储来优化能源使用。当设备处于待命状态时,可将剩余额度回收用于紧急情况下的启动,而非简单地让它浪费掉。同时,将常规配备硬件功能升级为软件定义功能,可以减少实际所需能源消耗,同时提升可扩展性——因为你可以轻松地添加更多节点而不会受到现有基础设施限制影响。
最后,与上述提到的所有这一系列改进相伴的一个重要因素,是持续教育与技能更新。一旦实现了真正意义上的自我学习/适应能力增强,那么原本看似不可预见的问题,就会成为日常工作中的平常事态。不仅如此,这种精神也是推动创新活动最直接来源之一,也许未来某天,即便面临无法预见的问题,我们也会发现自己已经准备好迎接那样的挑战,只不过当时还不知道怎么称呼它罢了!
总结一下,本文探讨了当前智能制造趋势下对于工控机电源提出的一些新挑战,如提高功率质量、保障数字安全、实现绿色节能以及促进持续教育等。在这样的背景下,如果想要成功实现“Industry 4.0”,那么必须不断完善我们的设计思路,并寻求既可靠又经济有效的手段以支持这一目标。