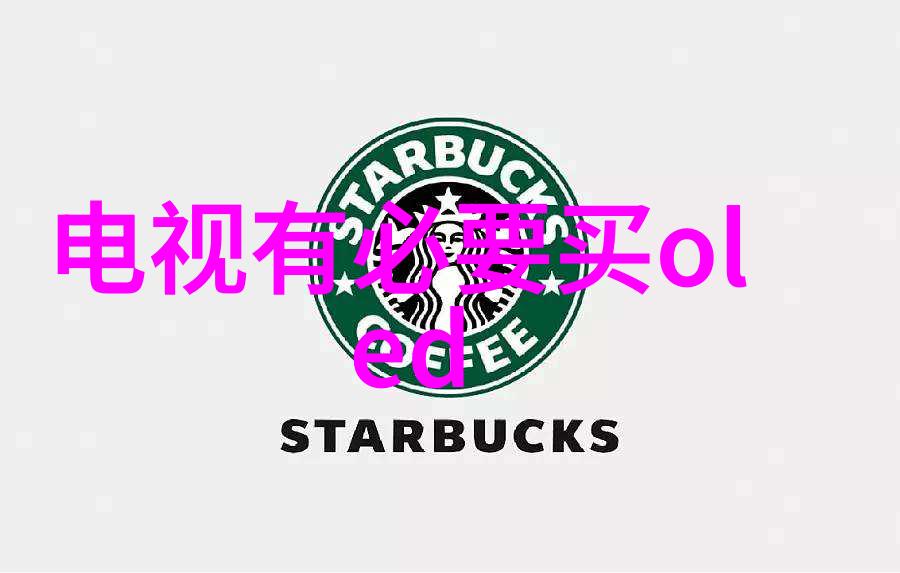
创新思维下的516s实践案例分析
在现代企业管理中,持续改进和效率提升已经成为企业生存与发展的必然要求。为了实现这一目标,不少企业开始采用五大件(5S)系统,即整理、清洁、组织、标准化和自律,这一方法被广泛认为是提高工作效率和降低成本的有效工具。但随着生产环境的不断变化,传统的5S不再满足新时代对质量和效率要求,因此有了6S,即将原有的5S基础上增加了一项“安全”元素,以此来更好地保证员工安全。
1. 五大件(5S)的基本概念
a. 整理(Seiri)
首先要进行的是整理活动,将所有不必要或多余的物品从工作场所中移除出去。这一步骤可以减少混乱,从而让员工能够更容易地找到所需工具和材料。
b. 清洁(Seiton)
接着进行清洁活动,确保整个工作场所保持干净整洁。一个干净的地面不仅能促进良好的身体健康,还能避免事故发生。
c. 组织(Seiso)
通过定期对工作站进行整顿,可以保持物品按类别分类并有序摆放,使得寻找物品变得更加高效。
d. 标准化(Shitsuke)
最后,要形成一种习惯,即每天坚持执行前面的四个步骤,并且制定相关规则及程序,让这些做法成为了员工日常作息的一部分。
2. 六大件(6S)的升级改造
随着市场竞争加剧,对产品质量的追求越来越高,同时也加强了对劳动者安全保护意识。在这样的背景下,“安全”这个新的“六”元素被加入到五大件之中,构成了六大件系统。
a. 安全性
在实施六大件时,将“安全性”作为核心要素,与其他五个步骤紧密结合起来,是非常关键的一步。这包括确保设备运行正常,无潜在风险,以及提供适当培训以防止意外伤害发生。
3. 六大的实践案例分析
现在,我们将举几个具体案例来说明如何在实际操作中融入这套系统:
案例一:
一家电子制造业公司发现,由于缺乏有效管理导致了频繁出现机器故障。因此,他们决定实施6S计划。在第一阶段,他们清除了所有无关设备,然后根据功能分类并标记每个区域。在第二阶段,他们建立了严格的维护计划,并定期检查设备状态。此外,他们还引入了一系列关于使用正确配备个人防护装备(PPE)以及遵守操作规范等教育项目。结果是生产时间延长了60%,同时事故数量显著减少,为公司节省了一笔可观的大额资金用于扩展业务范围。
案例二:
另一家食品加工厂由于卫生问题屡次遭受罚款,最终不得不重建其生产流程。他们采取措施重新评估其运营流程,并为其变革奠定基础。当他们实施6s时,他们首先删除或归还任何过时或损坏的工具,然后安装新的照明设施以提高视觉效果并减少光源误用。此外,该公司还设立了一项针对卫生标准及其遵守程度监督制度。此后,该工厂获得了ISO认证,并成功逃脱进一步处罚,其客户群体也因其优质产品而增加。
案例三:
最后一个典型示范是一个位于工业区内的小型机械制造商。他认识到尽管他拥有专业技术人员,但他的团队仍然存在许多浪费的问题,如失踪部件、高水平的人力资源投入以及低水平的事故频率。一旦应用到了基于创新思维策略上的六阶结构,他注意到他最主要的问题是在供应链上处理非标准化零部件导致需求无法得到快速响应。他解决这个问题的一个方法是采用预打印标签,以便更快地识别出哪些零部件属于哪种类型,从而简化库存管理过程。一旦这种流程稳固下来,就没有更多需要从库存箱子里挖掘它们的事情发生,更重要的是,它们也不再丢失,因为他们知道它们放在哪里。
结论
通过以上三个不同的行业背景下实际操作中的案例,我们可以看出,在不同情况下如何灵活应用六阶结构去解决各自面临的问题,这样的实践对于提升企业性能至关重要。而对于那些想要持续改进自身经营方式并创造价值的手段来说,不断探索新的方法和技巧总是一种明智选择。如果你想让你的组织走向卓越,那么把握住这一点就很关键。