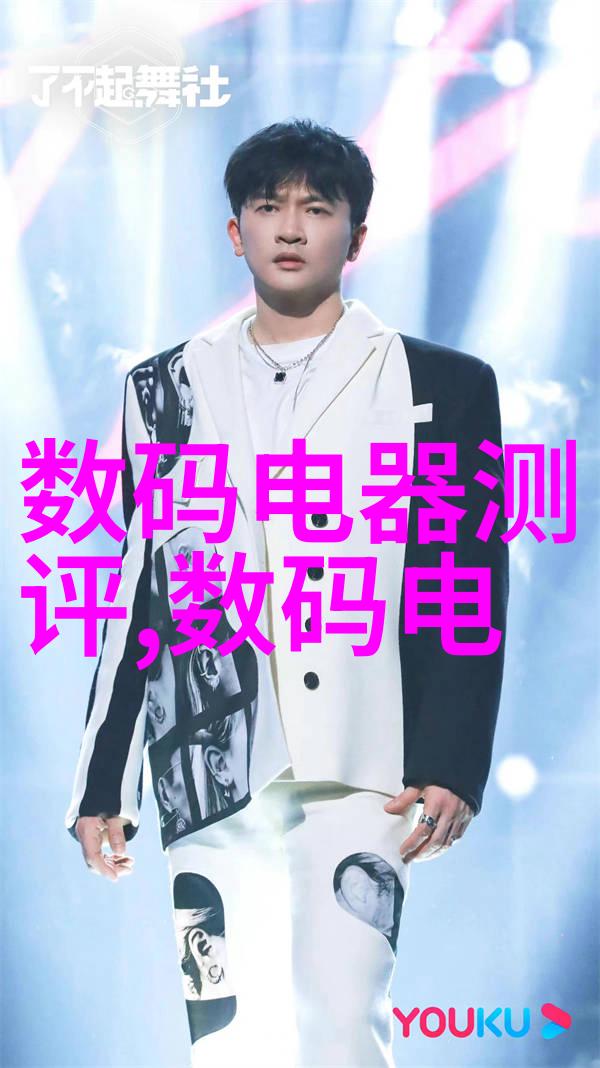
实施6s在制造业中的挑战有哪些
六大基本工具(五素)是日本的丰田公司提出的用于改善生产效率的一系列方法论,它们包括顺序(Seiri)、整理(Seiton)、清洁(Seiso)、标准化(Seiketsu),以及自我检查和持续改进(Shitsuke)。在全球范围内,这一系统被广泛应用于各行各业,尤其是在制造业中。然而,不同企业面临的具体情况和挑战也各不相同。
首先,在实施6s时,企业需要进行全面的评估,以确定当前的状态与目标状态之间的差距。这可能涉及到对现有的流程、设备、人员技能等方面进行详细分析。在这一过程中,企业往往会遇到一些难以预料的问题,比如员工对于新的工作方式或流程的抵抗情绪,以及管理层对于资源分配和时间投入所需额外努力的担忧。
其次,即使评估阶段已经完成,并制定了详细计划,但实际执行仍然是一项巨大的挑战。例如,在实践5S原则时,许多企业发现自己没有足够的人力资源来处理即将清理出来的大量废弃物品,或是没有合适的手段来回收这些废弃物品。此外,对于那些历史悠久且拥有大量老旧设备和过时设施的工厂来说,完全改变现状是一个长期而艰巨的任务。
再者,对于新加入团队成员来说,要快速掌握并融入新的工作环境并不容易。特别是在培训不足的情况下,他们可能无法迅速理解如何正确地执行6s规则,从而导致效率低下甚至安全隐患产生。此外,由于不同部门间沟通不畅或者领导层对该体系认识不足,有时候整个组织内部缺乏统一性的推动力,使得6s改革遭遇阻碍。
最后,还有一点需要强调的是,即便某个部门或一个小组成功地实施了六大基本工具,也不能保证其他部门或项目能跟上相同步伐。一种常见的情况是,一部分人士由于各种原因未能参与其中,而另一部分人士则因为缺乏连贯性质的人际交流而感到孤立无援,从而造成了一种“岛屿”效应,让整个组织难以形成真正的一致行动。
总之,无论是在规模大小还是行业类型上,都存在着多样化的问题和挑战。但正因为如此,每一个实现六大基本工具成功转型的案例都充满了宝贵经验值,可以为其他企业提供启发。通过不断学习、实践,并解决实际问题,我们可以逐渐克服困难,最终达到提高生产效率、降低成本、增强竞争力的目的。