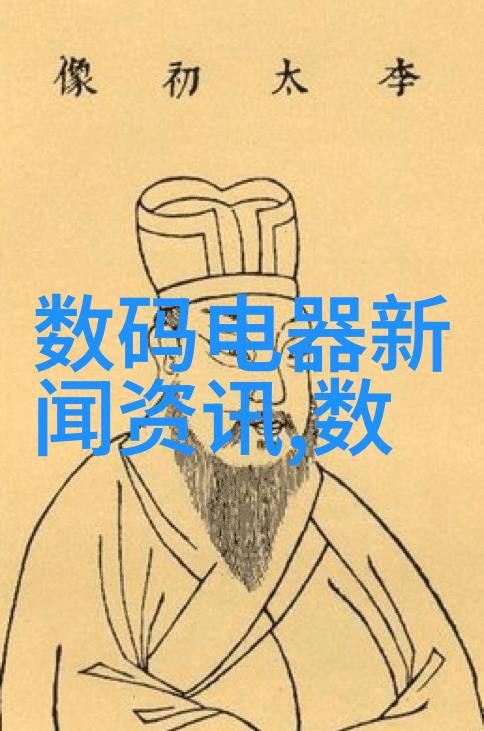
汽车冲压件材料利用率的提升之道乃是科技与智慧的结晶自动化软件技术为其指引灯塔
汽车冲压件材料利用率提升之道,揭示自动化软件技术的智慧
近年来,随着人们生活水平的不断提高,汽车需求量日益增长,各大汽车厂商之间的竞争愈发激烈。为了保持成本优势并提升品牌竞争力,不断推出新车型成为行业内的一项重要趋势。而与此同时,由于铁矿石和焦炭等自然资源日渐紧张,对提高材料利用率不仅有助于降低生产成本,还符合节能减排的环保理念。
工艺优化是实现这一目标的关键一环。在落料排样方面,我们通过优化模具设计,减少废料,使得原先只能开卷出一张板料而现在可以开出两张,从而显著提升了材料利用率,如对T6车型内纵梁模具进行优化后,可将原来的78.2%提高至87.6%。
另一种方法是合并材料规格,以减少钢材品种数量。每增加一种新规格钢材,都会造成库存管理上的额外负担。例如,将T6车型机罩外板由单独使用专用钢材改为采用X7机罩外板卷料制成,无需专门配备新的模具,大幅度减少了库存和管理成本,同时也提高了材料利用率3.7%。
在模具设计上,我们还采取了一模多件策略,即在一套模具上生产多个零件。B5车型机罩内板与T7门内板共用同一个模具,从而避免了单独制作加强板及锁座,加强了整体效益。此外,一些零件如MX3车型后门外板,可以通过调整设计,使其在一张毛坯中产生两个零件,而不是四个,这样做不仅节省了一部分工艺补充面积,还能进一步提高材料利用率4.16%。
对于毛坯尺寸,我们则倾向于控制其大小以最大限度地使用每块毛坢。这包括调整拉延筋位置、缩小开卷步距以及精确定位装置,以确保零件质量同时满足标准,并且能够有效地消耗掉所有必要的毛坯。此举使得T/B车型前风窗下横梁零件的物资消耗比原来高出了2.4%。
最后,在收集废料再次使用方面,我们发现许多未被完全利用的小片金属碎屑。如果能够将这些碎屑用于其他小零件或部件的生产,那么就可以避免单独采购这些组分,从而既节约成本又增加整体物资转换效率,如R33顶盖内部采用这种方式从侧翼内部获取表面余留切割成形后的初始圆盘状残余铝箔加工得到可用的矩形铝箔,这种操作使得R33顶盖工作时所需铝箔重量从最初11,993克降至9,494克,有13%以上节省,而且由于更轻便,也使得整个顶盖更加易于安装和拆卸,因此非常实用。
总结来说,通过这几种手段我们成功地提升了汽车冲压件的物资转换效率,让我们的产品更加经济高效,同时也符合环境保护要求,为整个行业提供了一份宝贵的心得教训。