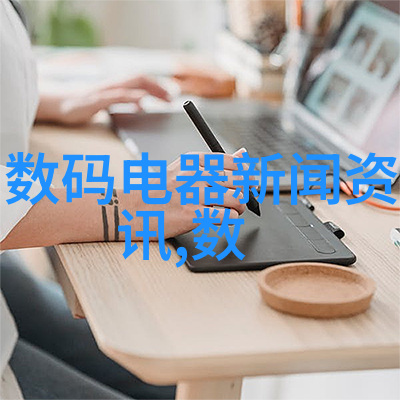
电动汽车中的转子油冷电机犹如心脏在体内跳动深度解读其工作原理
导语:本文详细阐述了油路设计中各关键因素的优化策略,并对多种方案进行了深入对比分析。本篇文章旨在解读其设计过程,期望为解决实际问题提供有益的启示。今天,我们将探讨电动汽车转子油冷电机方案的文献解读,文章全面介绍了油路设计中各个变量的优化过程,并对每个方案进行了详尽对比分析。本文深入剖析其设计流程,以期帮助大家更好地解决实践难题。一、油路布局首要任务是审视我们即将研究的电机油冷系统全貌,其核心结构如同图表所示。与传统设想相较,这项创新之处在于,在一般定子水冷体系基础上巧妙增添转子的冷却通道。这一布局确保从前盖引入冷却液,它先经过定子铁芯形成环形路径,然后通过后盖汇集至转子内部,从而再次回到前盖出口。
二、电机结构优化为了实现这一复杂布局,需精心打造电机前后盖和壳体,如同图例所示。在壳体轴向通道方面采用分段进出技术以减少阻力。此外,对于转子部件,我们采纳了一种特殊加工工艺,即分两段切割后重新焊接(关于该加工工艺,可查阅另一篇外文报告,该报告专注于轴摩擦焊技术,对需要进一步了解者建议关注作者微信公众号),转子的具体构造参见下图:
三、仿真迭代循环仿真基本步骤如下:基于双向耦合分析(温度场与磁场)进行反复迭代计算,从初始温度开始,再依据模拟结果调整温度值,最终达到稳态平衡状态。为了缩短仿真时间,本次实验采用2D数模来处理磁场,而3D数模用于温度场计算,其中换热系数参考经验值。
四、实际测量验证通过比较不同工作条件下的实际测量数据与预先建立模型中的理论值得出结论,例如2300rpm和7.38Nm工作状态下误差控制在10%以内。具体数据可见下列图表:
五、提升性能1. 选择合适的机壳通道形式针对不同的流量环境,每一种通道形式及其效果如同此处展示:根据系统流量和要求综合考虑后确定最优选项显然,在低流量时a到b明显提高绕组效率;c相对于b在高流量时则不及b,但结构更复杂;因此,在选择机壳通道时应结合流速考虑,以找到最佳匹配方案。
精准设置转子进出口角度随着需求可调整角度大小,如同以下几组特定角度所示并通过测试发现第三组为最佳配置。
六、测试方法实施样品开设六个单独的水循环通道,如图所示,并利用热敏电阻监测定子线包、中间铁芯以及壳体上的温度变化,同时由于无法直接测量转子的温标,一般使用带有标签纸记录法来估算其温标位置分布如下:
七、本次试验结果显示风冷80分钟内达到130℃未达平衡状态;单壳体加湿60分钟内达到110℃已达平衡;而壳体加轴同时也能30分钟内降至80℃并保持稳定。另外从时间维度观察,单壳体和轴同时加湿后的初期效果相当,但30分钟之后区别愈发明显且持续扩大。此案例与常规喷洒型或单层式空气涡轮涡旋式冷却方式相比较表现更加突出,如附录表格所示:
八总结最后,本案例不仅超越了传统风扇散热模式,更是在与其他传统水循环散热手段相比都取得了显著成效,比如线圈平均降低50%,甚至超过现行单层式散热器减少38%,使得这一新颖改良措施成为提高整车电子设备耐用性有效途径之一。