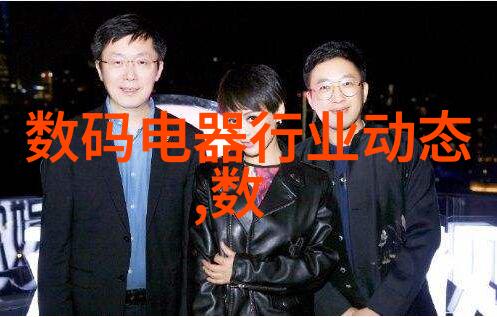
热塑钢管制造工艺解析
热塑钢管的生产流程
热塑钢管是通过高温下熔化成形的过程制成的一种复合材料产品。其生产主要包括原料准备、加热熔化、注射成型和冷却固化等几个关键步骤。在这些步骤中,高质量的原料选择对于最终产品的性能至关重要。
原料选择与预处理
在进行热塑加工之前,首先需要选购适宜的聚合物作为基材。根据不同的应用场景,可以选择不同类型和规格的聚合物,如PP(聚丙烯)、PE(聚乙烯)等。这些材料通常会经过严格筛选,以确保无杂质影响到最后产品的性能。此外,对于某些特殊需求,还可能需要对原料进行额外处理,如颜色着色或添加抗氧剂以提高耐久性。
加热熔化与注射模具设计
在开始热塑过程前,必须将所选材料加至一定温度,使其达到软化状态。这一步通常使用专门设计的小型炉灶或工业级的大型加热机器完成。在此期间,操作员需密切监控温度控制系统,以防止过度加热造成材料变质。
成型模具设计与精密控制
为了保证每一根钢管都能达到精细要求,模具设计得体非常重要。模具内部结构应考虑到各种尺寸和形状,并且要有足够的清洁性以避免残留物影响成品质量。此外,在实际操作中还需对压力、速度以及注入量等参数进行精细调节,以实现最佳成型效果。
冷却固化及检验标准
最后,当所有环节结束后,将完成形成后的钢管放置于专用设备中进行冷却固化,这个过程决定了最终产品是否具有良好的物理机械性能。一旦冷却完全,就可以对样品进行必要测试,比如硬度检测、拉伸强度测试等,以验证其满足特定应用标准。如果不达标,则可调整工艺参数重新制作直至满足要求。
随着技术不断进步,无论是新兴行业还是传统领域,都越来越多地采用这种能够提供优异耐磨性、高韧性的复合材料——即使面临极端环境条件下的挑战,这些高科技铝锡焊接件仍然展现出它们独特而坚不可摧的一面。