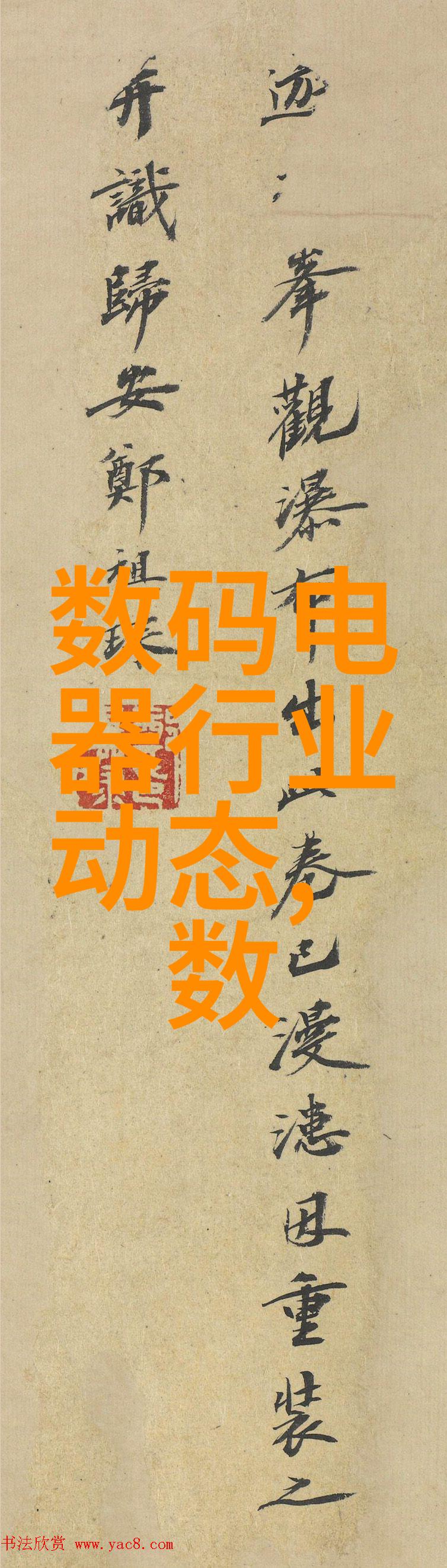
工控自动化以太网技术特性宛如现场总线系统中的巨龙威力无穷
工业自动化以太网技术特性:从现场总线系统到实时网络的飞跃
工业操控网络的演进
工业操控网络的发展是与控制系统革新同步进行的。控制系统经历了基站式气动外壳控制、电动单元组合式模仿外壳控制、集成式数字控制、集中控制、大规模现场总线(DCS)和近年来兴起的工业以太网(Industrial Ethernet)等六个阶段。早期基于基站式气动外壳和电动单元组合式模仿外壳仅仅改变了驱动方式,无法实现不同回路之间信息交流,每个回路是一个独立孤岛,不属于网络范畴。
随着计算机技术的进步,计算机被引入到控制系统中,它不仅能处理数据,还能够根据输入值、过程变量及其他测量值通过PID或高级算法生成输出值,实现对执行机构的直接控制,这就是所谓的人工智能化思维。会集型控制由于其结构简单,只面向操作对象,没有形成网络体系,但引入计算机后,使得高级算法得到应用;然而,由于出产流程复杂,软件开发需求巨大,而且软件结构杂乱无章,使得体系升级能力较弱;在多个回路上运行时,对实时性和可靠性要求难以保证。
真正意义上的工业操控网络是在70年代出现第二代计算机互联(DCS)的概念。它采用“集中管理分散操作”的设计思想,以适应高速通信协议,并逐渐形成了涣散化和层次化思维模式。在今天使用的大型DCS中,有环形、总线形和分层式几种架构。
尽管如此,大型DCS也有显著缺陷:
结构为多级主从关系,设备间通讯需经过主机导致负荷重且功率低,当主机发生故障整个体系崩溃;
还广泛运用模拟信号,如4-20mA电流模拟信号传输可靠性差,不易数字处理;
各厂家制定独立规范,通讯协议不开放,加剧了整合与应用限制,对跨国企业进一步开展不利。
为了克服这些瓶颈问题,便产生了现场总线技术,将操控功能下放至现场设备,同时提供全数字、高度互操作性的联网解决方案,是连接场地设备或场地界面的关键部分,与数据信息网融为一体推动自动化水平提升。
但FE也存在一些挑战:
现场总线标准众多且各有优势范围用户选择困难;
若同一局域网内有多种现场总线共存,由于不同标准造成通讯协定的混乱,无缝连接成为难题;
另外,在安全性、稳定性以及数据传输速度等方面还存在技能挑战或者不足以满足现代企业对信息要求的事实上各种技能都存在敞开性的不足或者条件性的敞开,因此提出基于TCP/IP协议的工业以太网技能解决这一问题。
以下详细介绍工业以太网技能特点:
工业以太网技能特色
由于其高速传输、高效能耗低安装便捷兼容好等优点在商业领域广泛应用近年来随着IT技术快速发展进入工控领域形成新的Industrial Ethernet 技术。这主要因为工控体系向分布式智能化方向发展需要一个开放透明的通讯协议支持。
2.1 工业以太_net 的优势
(1) 以太_net 是完全开放完全数字化遵循统一标准不同的厂家的设备可以轻松互联,
(2) 以太_net 能够实现 Industrial Network 与 Enterprise Information Network 无缝连接形成企业管治一体化全开放网络如图所示,
(3) 硬件成本低廉,因为 Industrial Ethernet 技术已非常成熟软硬件受到厂商高度重视并广泛支持有多种软件开发环境硬件设备供用户选择,
(4) 通信速率快跟随企业信息规模扩大与复杂程度增加对信息量需求日益增长甚至需要音频视频数据传输现在已经开始应用10M 100M 快速Ethernet 千兆Ethernet 技术也逐渐成熟10G Ethernet 技术正在研发其速率远超现有的现场总线,
(5) 可持续发展潜力大在瞬息万变的地球上公司生计与开展将依赖于快速有效通讯办理 网络资本技巧与通讯技巧不断迅速老练确保Industrial Ethernet 技术不断前行。
2.2 工业_eithernet 面临的问题
2.2.1 实时性能问题
在 industrial control 系统中即使是最短时间内完成某事物反应也是必需品。而 industrial 对数据传递的一致要求极高往往数十毫秒内更新。而同样因选用CSMA/CD介质访问方法,即非实时方法当发生冲突必须重发而可能尝试16次之多付出时间代价此策略很难满足 industrial control 需求尤其是掉链条即使只是几秒钟就会影响整个生产乃至人身安全事故这样的延迟不能接受;
以上提到的所有问题目前均已得到部分或全部解决:
交流方式提高效率避免干扰降低误码概率改善整体性能;
交叉交替调度减少竞争提高带宽利用比降低排队延迟;
同步通信减少碰撞次数增强服务质量;
去噪滤波器消除干扰信号增强接收质量;
优先级调度确保关键任务及时完成保障重要业务顺畅运行;